Electropolishing Applications Guide
Spark Steel is also having huge & ready stock of Stainless Steel 304 Electro Polished Pipes,Stainless Steel EP Pipes,Electro Polished Pipes,we at Spark Steel exporting Stainless Steel 304 Electropolished Tubes since 2 decades,Spark Steel is largest stockiest & exporter of Stainless Steel 304 Electropolished Pipes in India.
Classification
Stainless Steel AP Pipe
Precision stainless steel tube often occurs oxidation layer in colors of black or yellow during processing. AP pipe emerges as the ideal solution to this problem by utilization of pickling and passivation, thus further enhancing steel appearance and corrosion resistance.
electropolishing is successfully applied to an expanded range of new applications:
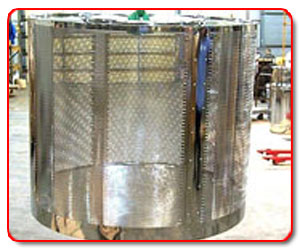
- Pipe/Tubing
- Valves
- Fittings
- Sheet Metal
- Stampings
- Spinnings
- Weldments
- Castings
- Wire Goods
- Forgings
- Fasteners
- Drawings
Major benefits of electropolishing continue to be demonstrated in reactor vessels, heat exchangers, blenders, storage tanks, piping and tubing, clean rooms, food and beverage processing equipment, medical equipment, machined parts and nuclear applications. See the sections below to find the advantages electropolishing offers for your application.
Electropolishing Reactor Vessels, Heat Exchangers, Mixers, Agitators, Blenders & Storage Tanks
- Extends operating times and reduces wear and tear on parts.
- Reduces adhesion and contamination on the surfaces of process equipment. (Electropolished surfaces perform as well as glass surfaces in many applications.)
- Promotes easy cleaning and reduces associated downtime.
- Significantly reduces a metal's tendency to corrode.
- Reduces friction between moving metal parts.
- Improves heat transfer efficiency in heat exchangers.
- Enhances flow characteristics of piping and tubing.
- Eliminates burrs from machined parts.
- Reduces surface stresses in formed metal parts.
- Lengthens metal life against sour gas.
Experience tells us that any container used in mixing, blending or storage processes for liquids or powders is an excellent candidate for electropolishing. The non-stick qualities of an electropolished surface have obvious advantages in these applications. Companies who have used electropolished parts successfully in the above applications include ExxonMobil, Shell, Dow Chemical, BASF, Air Products & Chemicals, Inc., Dupont, Albemarle, Solutia and many others.
Piping & Tubing
In recent years, electropolishing has been shown to provide the ultimate I.D. and O.D. finish for piping and tubing. Electropolishing is necessary whenever non-contaminating, non-particulating and anti-fouling surfaces are required. In addition, pipe and tubing also benefit from the minimal friction and maximum purity aspects of electropolishing. Major beneficiaries of electropolished piping and tubing include the petrochemical, nuclear, pharmaceutical, semi-conductor and food and beverage industries.
Clean Rooms
Clean rooms demand non-contaminating and non-particulating surfaces. Electropolishing is the ultimate finish for clean room tables, chairs, waste containers, light fixtures, exposed electrical conduit and outlet boxes, manufacturing and processing equipment, and other metallic components used in this application.
Food & Beverage Processing
Electropolishing provides the smooth, easy cleaning and cosmetically pleasing surfaces demanded by this industry coupled with unmatched non-contamination and sanitary qualities. The process reduces oxidation and contamination of stainless steel components used in kitchen, dairy and automatic food processing equipment, and descales food and beverage containers. Overall, one can expect a significantly cleaner surface that resists the contaminating build-up of undesirable bacteria and product particles.
Medical Applications
For many years, the medical field has been a beneficiary of electropolishing. All hospital, medical and surgical equipment (scalpels, clamps, saws, bone and joint implants, prosthetic devices, burn beds and rehabilitation whirlpools) should be electropolished to facilitate cleaning and achieve high levels of non-contamination. All metal articles exposed to radiation and requiring regular decontamination are prime candidates for electropolishing.
Machined Parts
All screws, bolts, washers, valve stems and bodies, and other machined parts benefit from electropolishing. The process provides a number of advantages, including deburring and stress relieving of the surface, easy clean up, a non-stick, non-contaminating, non-particulating finish, and a pleasing cosmetic appearance. It has been demonstrated that machined parts of electropolished 304 stainless steel exhibit superior corrosion resistance when compared to the same parts fashioned from non-electropolished 316 stainless steel. Precise machining using electropolishing techniques is an advantage in many applications.
Nuclear
Electropolishing is a critical finish in the nuclear industry. Used to polish surfaces located in radioactive environments, electropolishing reduces contamination pick-up and increases the effectiveness of conventional decontamination techniques. The process can be used to decontaminate radioactive metallic surfaces to non-detectable levels. Any contamination located on or embedded in the surface can be removed by the electropolishing process. In addition, residual contaminated electrolyte can be removed in the rinsing operation. A very effective application for electropolishing is the polishing of nuclear plant recirculation piping for stress-relief of internal surfaces that have already been mechanically polished.